Travelling automatic supply system
Greatly upgrading material stability of melt:
Currently the melting operation employs one to one, in case of lack of material, material filling is made by manually. When filling material into melting furnace, it may cause a fast melting temperature lost (20c-50c), this causes unstable die casting temperature and difficult controlling of casting parts quality. However, when applying Central Melting System combined with Automatic Supply System, its effectively improves temperature loss problem and upgrading quality qualification percentage for casting parts.
Reducing material loss and cost during melting:
Generally, material loss percentage by using conventional melting process is 3%-5% approximately. Therefore, when using Central Melting Furnace with its large closed type melting capacity, the contact area between melt and air is reduced, and hot air distribution is much more uniformity. Nowadays, the conventional melting furnaces employs an open type heating method, and heat conductivity is less than 15%. Central Melting System employs an advanced design - closed reflective heating system, its featuring great heating conductivity rate up to 30%, which means you will save approximate 50% melting costs.
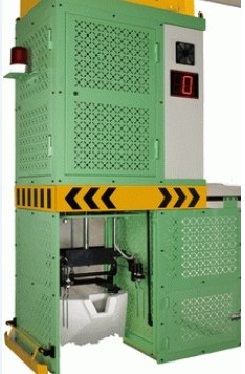
Unmanned、fully automatic melt supply
- Improvement of melt materials stability
- Ideal for die casting automation and unmanned operation
- Overhead travelling structure, space saving and great efficiency design
- Continuous, tightness, smooth, high temperature resist and safety rail
- Melt supply capacities from 5-15 stops of die casting machines
- Lack signal of material display and automatic supply
- Advanced multiple transmission devices for high sensitivity signal
- PLC controller for maximize operation convenience
- Buzzer sounds and warning light flashes when motion occurs
- Reduces material lost and melt temperatures difference during melting processes